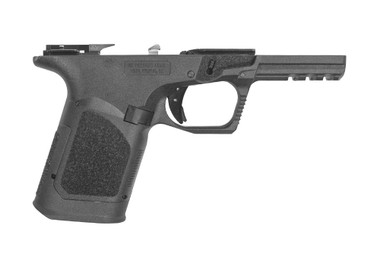
BUILD AT HOME
80% Arms sells AR-15 and .308 80% Lower Receivers, 80% Lower Jigs and other accessories which allow you to legally build a firearm at home in most states.
INCREDIBLY PRECISE
We utilize state of the art 5-axis CNC machines to mill all our .308 and AR-15 80 percent lower receivers to incredibly precise tolerances using premium billet aluminum.
RIDICULOUSLY EASY
We also offer our patented AR-15 and .308 Easy Jigs® which is the first 80% lower jig that makes it ridiculously easy for a non-machinist to finish their 80% lower in under 1 hour with no drill press required.
100% SATISFACTION GUARANTEED
Products manufactured by 80% Arms carry a lifetime warranty against manufacturing defects. We will promptly replace or repair any product that we determine to be defective.
START A NEW 80 LOWER BUILD WITH 80% ARMS
Featured Products
Build at home
80% Arms sells AR-15 and .308 80% Lower Receivers, 80% Lower Jigs and other accessories which allow you to legally build a firearm at home in most states.
incredibly precise
We utilize state of the art 5-axis CNC machines to mill all our .308 and AR-15 80 percent lower receivers to incredibly precise tolerances using premium billet aluminum.
ridiculously easy
We also offer our patented AR-15 and .308 Easy Jigs® which is the first 80% lower jig that makes it ridiculously easy for a non-machinist to finish their 80% lower in under 1 hour with no drill press required.